Machine Support Frame
Client: MECAL
The Dutch company MECAL designs, produces and installs Machine Support Frames (MSF’s) for the semiconductor industry. An MSF frame has to provide a stable, elevated base for the production machine that is placed on it. Normally an MSF is rigidly connected to the fab foor. This results in the same low vibration levels as on the fab foor as well as a very high stiffness for (inertial) forces generated by the machine.
Support Frames
Driven by Moore’s Law, production machines in the semiconductor industry will get more and more accurate. As a result, MECAL sees a demand for support frames with active vibration isolation. The challenge is to provide a robust isolation solution for machines with large moving masses, such as heavy stages or automatic loading unit. A soft suspension gives good isolation, but will suffer from severe sagging under varying loads. Since the MSF and the machine are separate systems, feed forward cannot be used.
MECAL developed novel active isolation techniques to provide isolation and stiffness in a very robust system for the machines in the semiconductor fab. An example of such a machine is a Scanning Electron Microscope, weighing 3500 kg and equipped with an automatic loading unit. To test these techniques MECAL turned to Controllab, because a rapid prototyping platform was required to measure the performance of an active controlled frame and test novel control strategies.
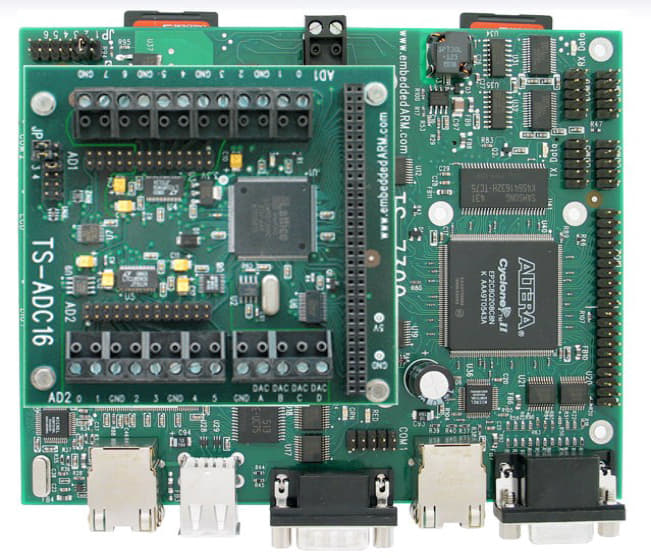
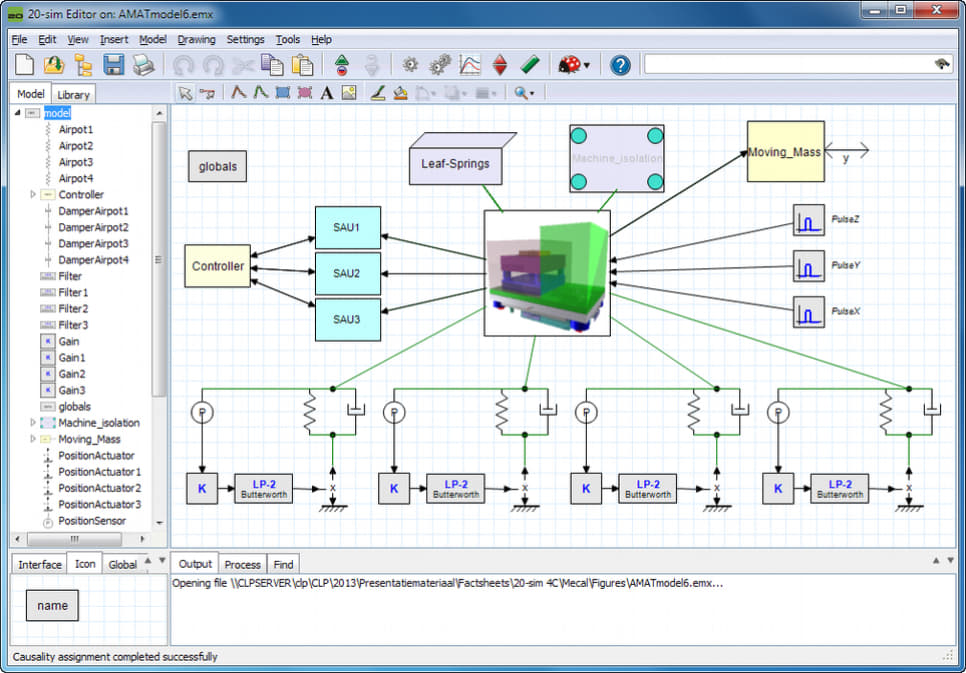
Rapid Prototyping
Controllab distributes a rapid prototyping platform that allows users to start with relatively little costs in the early phases of the project and scale up when the prototypes turn out to be successful. The platform consists of the software 20-sim and 20-sim 4C and various hardware products.
The project was started with a test-setup with four air- mounts which were actively controlled. For the controller hardware, the TS-7300 single board computer from Embedded Arm was chosen. This device is equipped with an ARM-9 processor with a Real-Time Linux OS and an FPGA for reconfgurable hardware. An additional IO-card was stacked on top to allow more IO connections with air valves, pressure sensors and accelerometers.
20-sim was used for modeling and simulation of the vibration controllers. The controller models were automatically exported as C-code to 20-sim 4C. With this package the C-code can be deployed on various types of hardware with a few clicks. This allowed MECAL to use the inexpensive TS-7300 hardware at the early stages of the project and change to more expensive industry proven hardware at a later stage, without any extra effort.In a series of quick iterations, controllers were designed and tested. Measurements showed that the concepts did work as expected.
Design Isolation Frame
The results from simulation and the frst real world tests with the TS-7300 controller provided the right information to design a vibration isolation Machine Support Frame for a client. An extensive design concept was devised and verifed using the 20-sim model. For the controller the Bachmann M1 industrial controller was selected. This M1 controller is also supported by 20-sim 4C, so the rest of the model-based design chain could be kept intact. The resonance modes of the real frame with payload were identifedusing frequency sweeps and FFT transforms on the response data, and used to validate the frame model in 20-sim. With this data, the controller was tuned to suppress noise in the desired low frequency ranges.
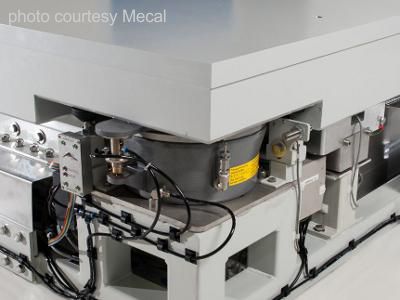
Results
The results turned out to be well according specifcations (isolation, stiffness, robustness). Using a model based tool chain with 20-sim
software and various types of hardware, allowed MECAL to show in a few weeks that the concept was viable.