Pipe Dropping
Client: Allseas
The Swiss-based Allseas Group S.A. is a global leader in offshore pipeline installation and
subsea construction. The group, with its own feet of specially designed ships, one of the
largest in the world. Allseas was founded in 1985 and has extensive experience in
construction projects around the world. One of the offces of Allseas is located in Delft. From
this offce a project was driven for laying pipes in the Gulf of Mexico. A necessary part of
obtaining this project was a comprehensive safety study. This safety study should demonstrate
that the ships used by Allseas and their methods of pipelaying, would operate within standard
safety limits.
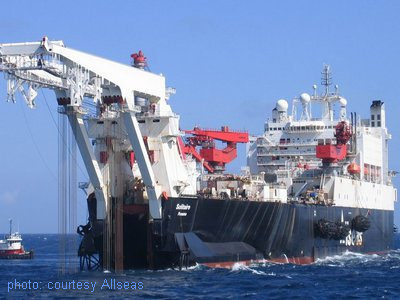
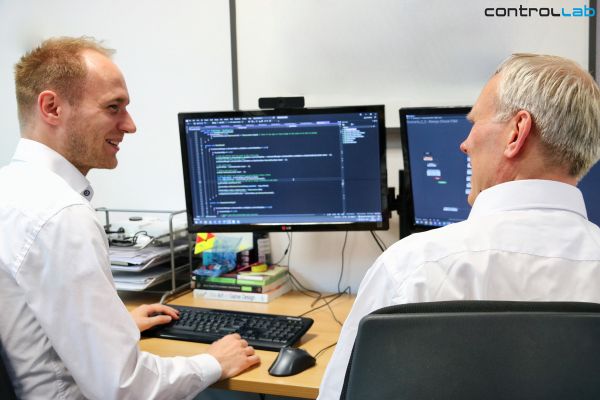
Risk Assessment
One of the critical notes of the contractor on this study was the problem of pipe rupture. During the laying of a pipeline, the pipe segments are connected with each other on a ship, and put as a strand into the water. If something goes wrong during the transfer, there is a risk that the whole strand will fall overboard and disappear into the depths. During the connection of the segments, there is crew on deck. The client wanted a risk assessment for the crew during a segment break.
Modeling
The risk assessment was made by Allseas using a dynamic model, which displays the movements of the pipe segments, if a break occurs. For the simulation, the package 20- sim was used. During the modeling, an exponential increase in simulation time per pipe section was found. Therefore, Controllab was asked for help. Analysis of the model showed singularities in the internal transformations of each pipe segment model. These singularities made a direct calculation of the model impossible, forcing the integration routines to fall back on an iterative solution of every simulation step. With a different mathematical description the singularities could be avoided and made the model useful.
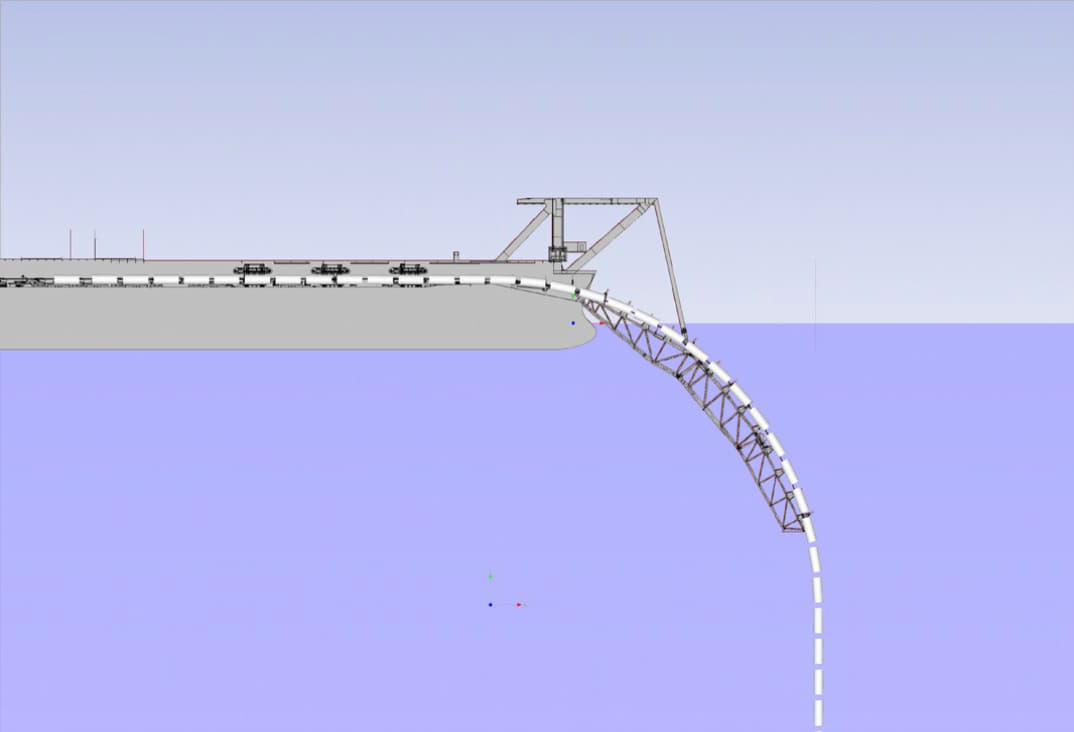
Approach
The package 20-sim allows various forms of model compilation. By clever using this, the simulation could be accelerated. The result was a model with 2642 variables, 208 independent states and 83 dependent states.Depending on the desired accuracy, a simulation run would take between 1 and 10 minutes. With this result, Allseas could run a number of scenarios within a short time period, and visualize the results with animations. This was used to effectively demonstrate that the crew on deck was safe during a pipe brake in any segment.