High-tech systems
In the high-tech systems market, there is a continues drive to create machines with more accuracy, higher speeds, and disruptive technologies. This requires advanced control systems which use multiple sensor inputs and machine models to calculate the optimal steering of the actuators. Controllab has developed the modelling and simulation package 20-sim, which is excellently suited for model based design. Using scripting and design environment was created with a high degree of automation. Controllab provides digital twins to develop and test these control systems.
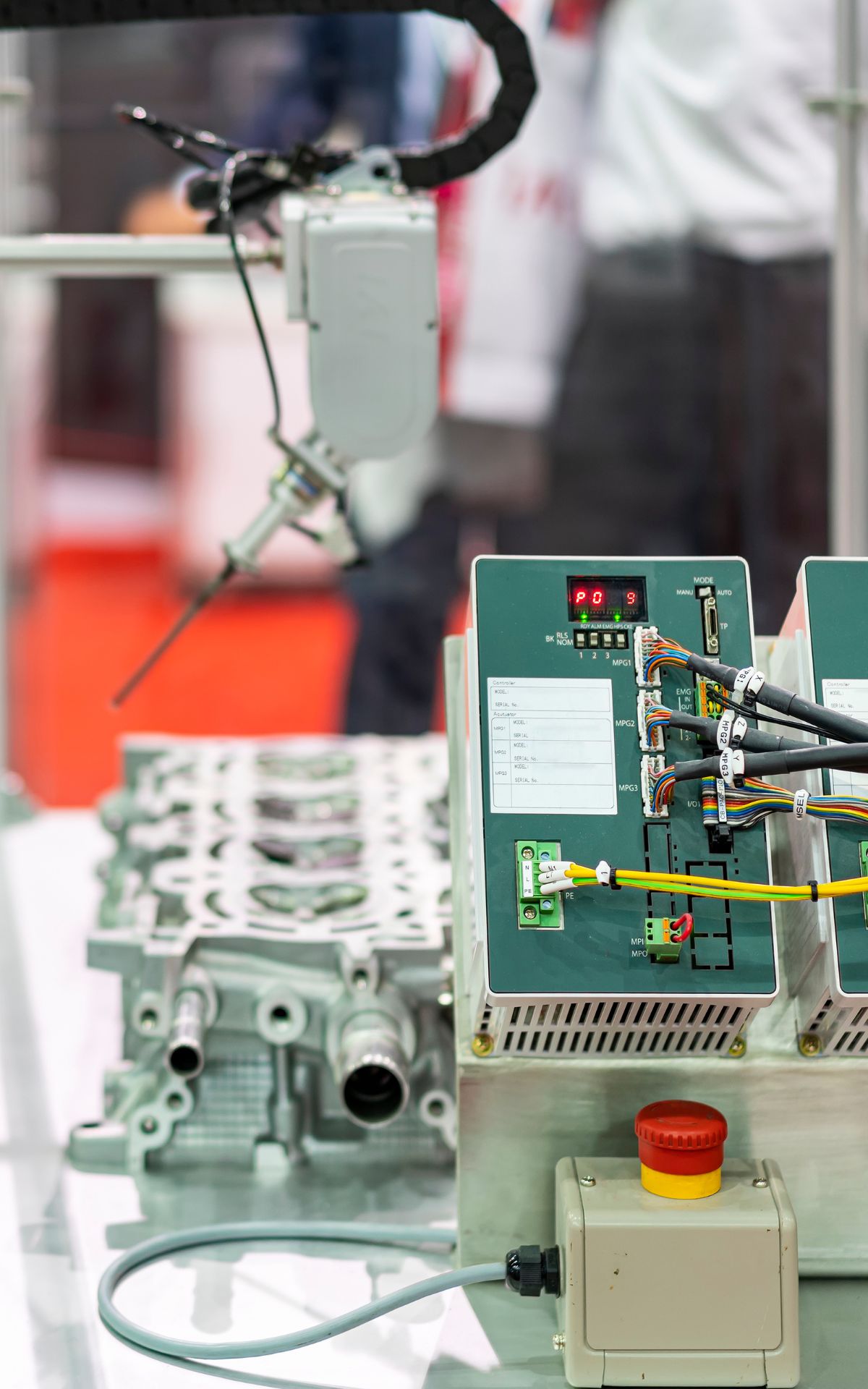
Digital Twins for high-tech systems
At Controllab, we’ve developed technology that quickly converts CAD drawings of machinery into dynamic digital twin simulation models. Our expertise extends to the creation of accurate simulation models for cranes, hoists, ladles and all other essential tools used in steel handling operations. These digital twins are an integral part of Steel Sim VR’s advanced simulators tailored for the steel industry.
A notable success story is Tata Steel’s Port Talbot steelworks, which used a Steel Sim VR simulator to train crane operators on a new charging crane to be installed a year later. The simulator, equipped with an authentic crane chair and a mock crane cabin with multiple LCD screens, allowed the operators to familiarize themselves with the new controls and behavior of the modern crane. This proactive training approach received positive feedback and significantly reduced potential start-up issues related to operator skills.
By using our digital twin technology, the steel industry can increase training efficiency, improve safety, and ensure seamless integration of new machinery.
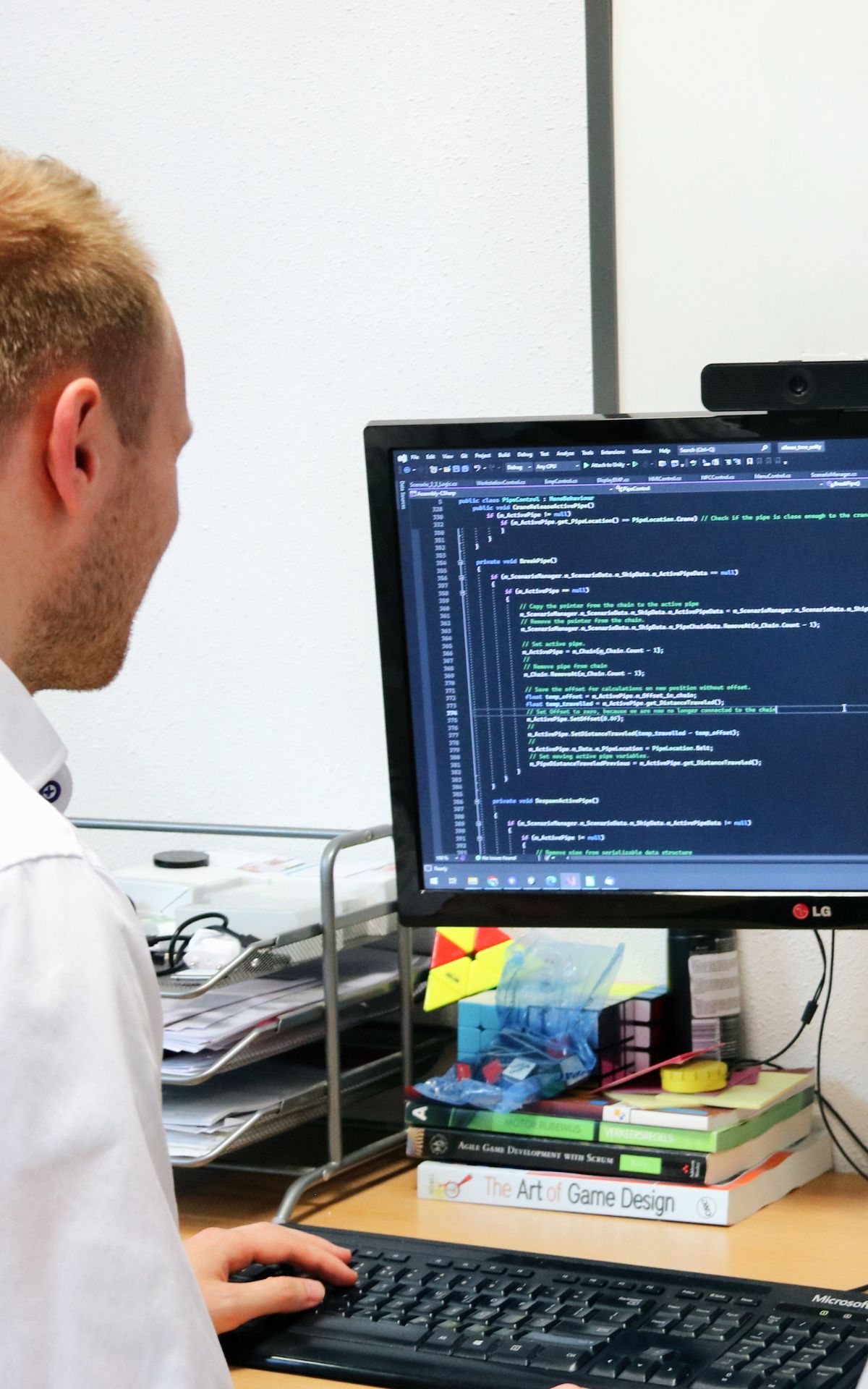
Control software
Our HIL (Hardware-in-the-Loop) simulator, a digital model, is a crucial asset for testing and fine-tuning new software in the steel industry. Specifically designed for initial software testing of cranes, it simplifies the complex process of understanding software rules and parameters, providing immediate visual feedback on any changes. This intuitive approach enables new software engineers to learn on the job, allowing them to experiment and make mistakes without severe repercussions.
At Controllab, we are experts in running these simulation models in real-time, seamlessly integrating our digital twins with control software. This capability allows our digital twins to operate as if they were the actual machines, making them ideal for developing and testing control software. Known as HIL simulation, this technology ensures that our digital twins provide a realistic, risk-free environment for software testing and operator training, significantly enhancing safety and efficiency in steel production.
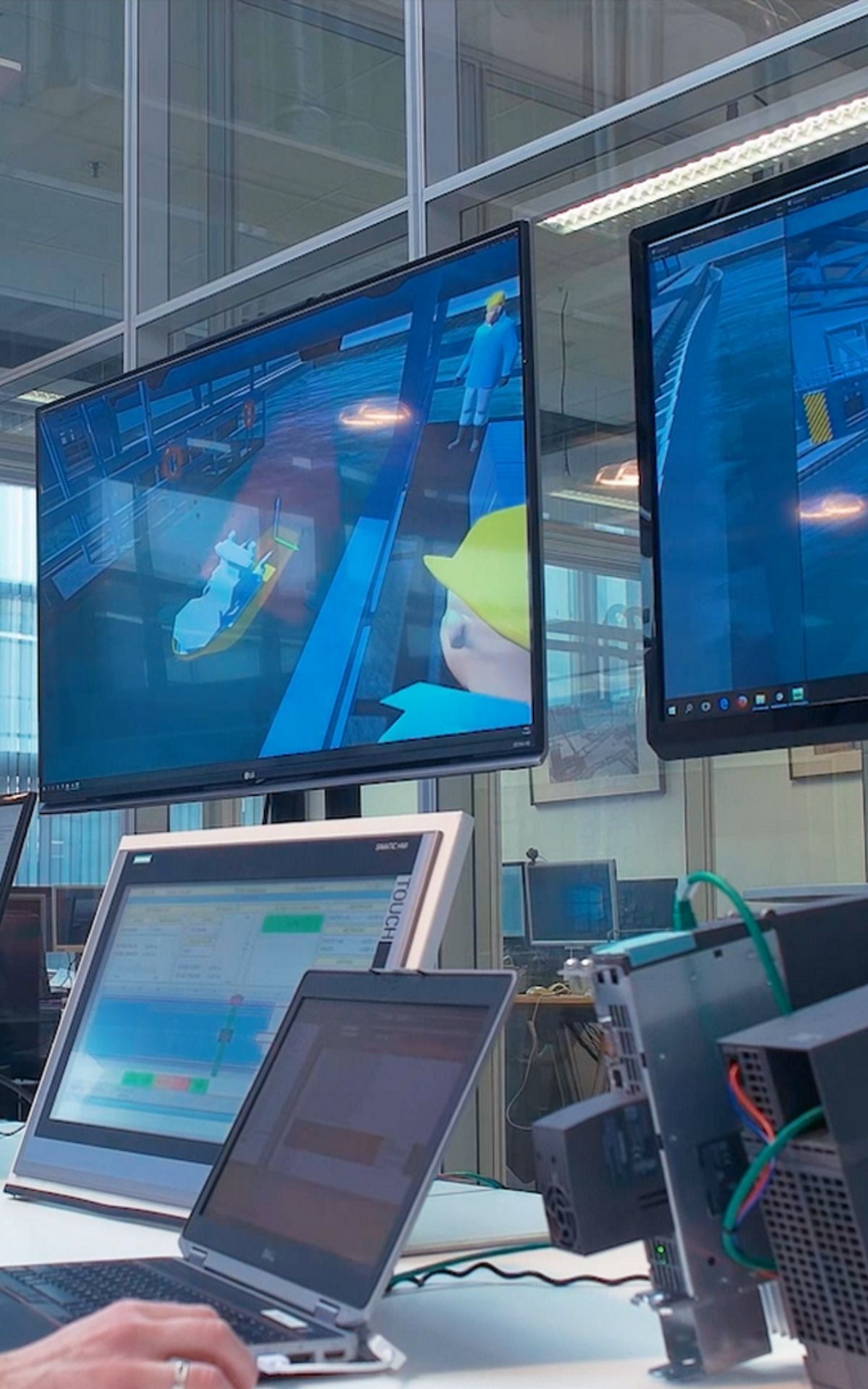
HIL Simulation
With our advanced digital twin technology, you can test virtually every aspect of machine operations, including scenarios that are too expensive or dangerous to replicate on real equipment. This comprehensive testing capability ensures higher quality and reliability in your processes.
Our training simulators provide a highly realistic experience, allowing for the adjustment of variables such as weather and other conditions. This flexibility bridges the gap between virtual and real-world training, offering a safe and cost-effective environment for trainees. By using our digital twin technology, trainees can practice repeatedly without the fear of real-world consequences—if a mistake is made, simply restart the simulation and try again. This reduces stress for the trainees and significantly cuts down training costs.
In summary, our digital twin technology not only enhances the quality and safety of software testing and operator training but also brings tangible cost savings and reduces operational risks.