Wind Tunnel Robot
Client: DNW
The German-Dutch Wind Tunnels (DNW) is a non-proft foundation under Dutch law. DNW operates its own Large Low-speed Facility (LLF) and the aeronautical wind tunnels of the German Aerospace Center (DLR) and the Dutch National Aerospace Laboratory (NLR). These wind tunnels are located in Germany and the Netherlands. The main objective of DNW is to provide the customer with a wide spectrum of wind tunnel test and simulation techniques, operated by one organization, providing the benefts of resource sharing, technology transfer, and coordinated implementation of research and development results.
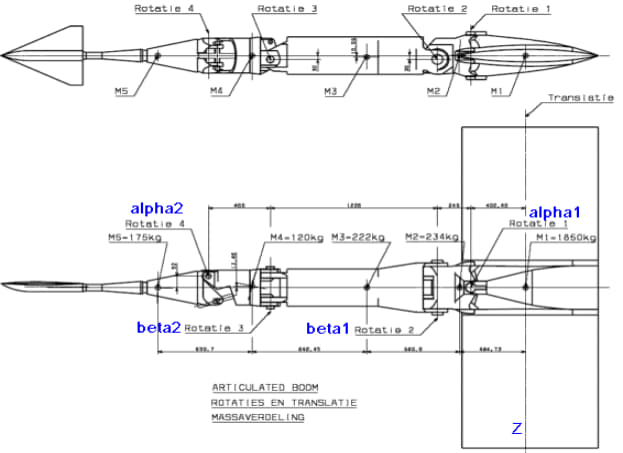
Robot
DNW serves customers from different market areas with appropriate wind tunnel test and simulation techniques. The test spectrum of the facilities comprises aerodynamic and aero-acoustic testing of fight vehicle models of aircraft, space craft, cars, etc. The applied test techniques cover a wide range of applications from steady and unsteady aerodynamic measurements, noise and fow measurements, engine and ground effect simulation to captive trajectory systems, drop tests and re-entry tests. In Amsterdam DNW operates a high speed wind tunnel. In this tunnel an area of 2.0 m x 1.8 m is available for testing from mach ranges of 0.1 up to 1.35 and pressures ranging from 0.2 bar to 4.0 bar. A robot is used to maneuver models into the test area
and keep them in the correct postures. For a tunnel redesign a new robot was
needed with improved maneuvering
capabilities and dynamic posturing. Controllab Products B.V. has been commissioned to create a virtual prototype of the robot to test the capabilities of the designed robot under dynamic wind loads. Because this project is classifed, this factsheet shows a virtual prototype of the existing robot, which was used to test the validity of the used design methods.
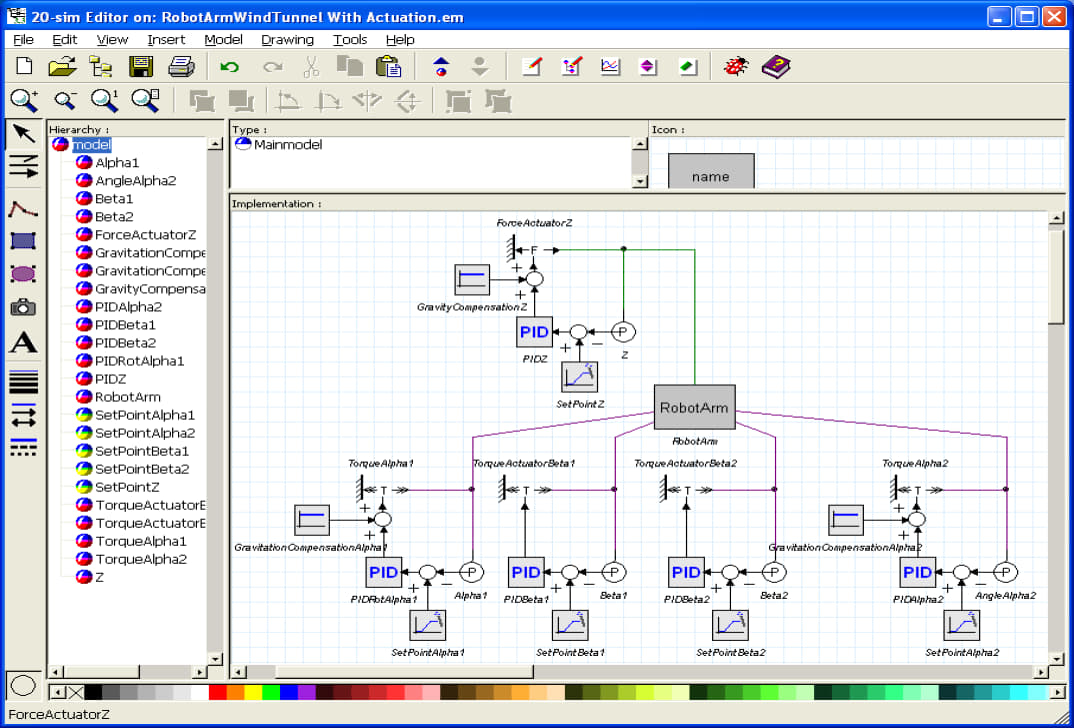
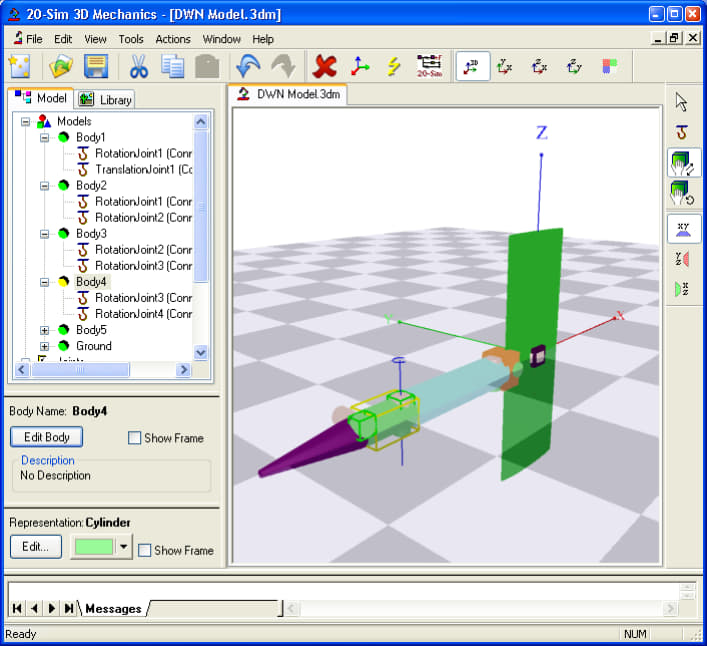
Modeling
A start was made by collecting the geometric data and physical parameters of the robot (i.e. lengths, masses, inertia parameters etc.). using these parameters, a 3D model was created using the modeling and simulation package 20-sim. The package allows you to enter 3D mechanical models by giving the position of joints, mass parameters etc. out of this data, a dynamic model is automatically generated. During simulation this models use the joint torques and wind loads as input and returns the corresponding motion of the
robot as outcomes. The validity of the model is ensured by using the physical laws of motion as a mathematical framework for thegeneration of the dynamic model.
The dynamic model can be coupled to standard library blocks of 20-sim, describing the electric actuators of the robot, the actuator amplifers and the connected computer control loops. In this way a virtual model is created that will mimic the forces and movements, of a real robot with a high degree of accuracy. Any variable that is inside the model can be shown in the plots. This allowed Controllab Products to plot the joint motor torques and currents as a function of a predefned motion profle of the robot. The profle was taken from a fle that is used for the real machine. The simulated torques and currents could be compared with the measurement results, verifying the validity of the concept.
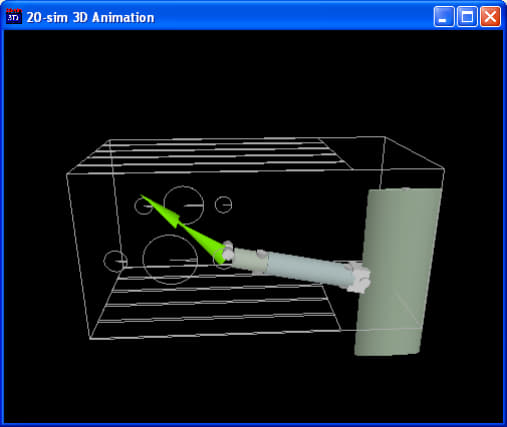